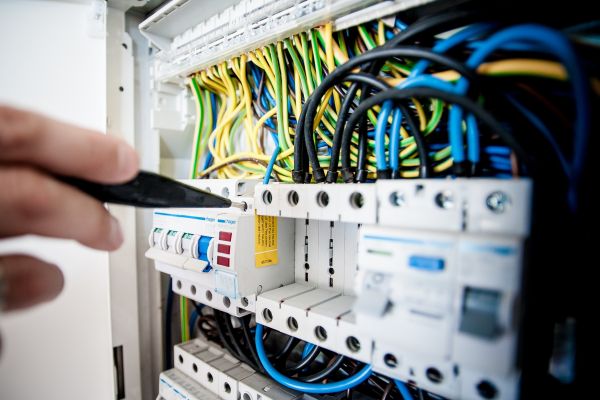
Como minimizar riscos no setor de elétrica
Como minimizar riscos no setor de elétricaQuando se trata de segurança do trabalho no setor industrial, as empresas do segmento devem priorizar ações que incluam a segurança no setor de eletricidade, com a preocupação de como minimizar riscos no setor de elétrica. Infelizmente, os acidentes de trabalho relacionados a choques elétricos no local de trabalho ainda são muito comuns – não apenas na construção e ambientes industriais pesados. De acordo com dados fornecidos pela Fundação Coge (Comitê de Gestão Empresarial), com base no ano de 2008, de cada 100.000 trabalhadores ligados ao setor elétrico, 14,8% foram considerados acidentados fatais. Segundo o relatório de estatística de acidentes no setor elétrico brasileiro em 2008 também fornecido pelo Coge, o Brasil apresentava 77 empresas no segmento, registrando 101.451 empregados próprios, 851 acidentes típicos com afastamento do trabalhador, 126.333 empregados terceirizados e 1.589 acidentados terceirizados com afastamento.
Para reduzir satisfatoriamente os riscos de acidentes que muitas vezes são fatais, são necessários alguns cuidados extras por parte das companhias e dos empregados. O primeiro deles é a identificação de riscos elétricos, o que propicia com maior facilidade a elaboração de ações que visem à diminuição de acidentes e, por consequência, os afastamentos dos trabalhadores, bem como reduz os índices de paralisações na produção por falta de funcionários. Por exemplo, fios desgastados ou rachados, um ligeiro odor proveniente da queima de painéis ou transformadores ou equipamentos, podem ser sinais bem claros de que algo não está funcionando como deveria, seja por falta de manutenção adequada ou por outros fatores.
Embora essas condições pareçam, a princípio, ser relativamente inofensivos ou não tão urgentes para serem resolvidos, o fato é que eles representam um sério risco de choque elétrico ou incêndio – um risco que pode e deve ser evitado. Mas como? Através de uma abordagem de senso comum que inclui tais fatores:
– Formação do empregado – a empresa precisa garantir que todos os funcionários receberam treinamento de segurança adequado em relação ao trabalho que eles desempenham – uma ampla formação em segurança elétrica deve sempre ser incluída no planejamento de manutenção. Se for o caso, contratações de empresas especializadas nesse tipo de treinamento, com workshops e palestras, é um fator a ser pensado com seriedade pelos gestores das indústrias. Vale lembrar que a prevenção de acidentes é bem mais fácil do que arcar com os custos deles, especialmente considerando o afastamento do funcionário, o que prejudica intensamente a produção.
– Conscientização – Embora haja normas reguladoras que exigem o uso de EPI’s, os equipamentos de proteção individuais, muitos empregados não os utilizam por vários motivos, e o que acaba falando mais alto é a negligência com a própria saúde. Nesse caso, é papel das organizações e seus gestores programarem palestras visando à plena conscientização de seus colaboradores, salientando a importância do uso dos EPI’s para a qualidade de vida dos empregados.
– Inspeções – Inspeções elétricas são necessárias tanto para os equipamentos antigos quanto os novos. As inspeções não chegam a ser uma espécie de manutenção, mas são ações preventivas com o objetivo de estar sempre atento a qualquer tipo de sinal que a máquina possa dar sobre seu desgaste, quando pode apresentar riscos de acidentes.
– Manutenção Planejada – Os reparos em máquinas e programas de manutenção planejada, entre outras ações de manutenção, levando em consideração os requisitos de manutenção são algo extremamente importante nas empresas e indústrias. A manutenção planejada evita acidentes e ainda contribui com a redução de custos, além de aumentar bastante a confiabilidade dos equipamentos, consequentemente, tornando a organização ainda mais competitiva e produtiva no cenário econômico.
Nenhum comentário